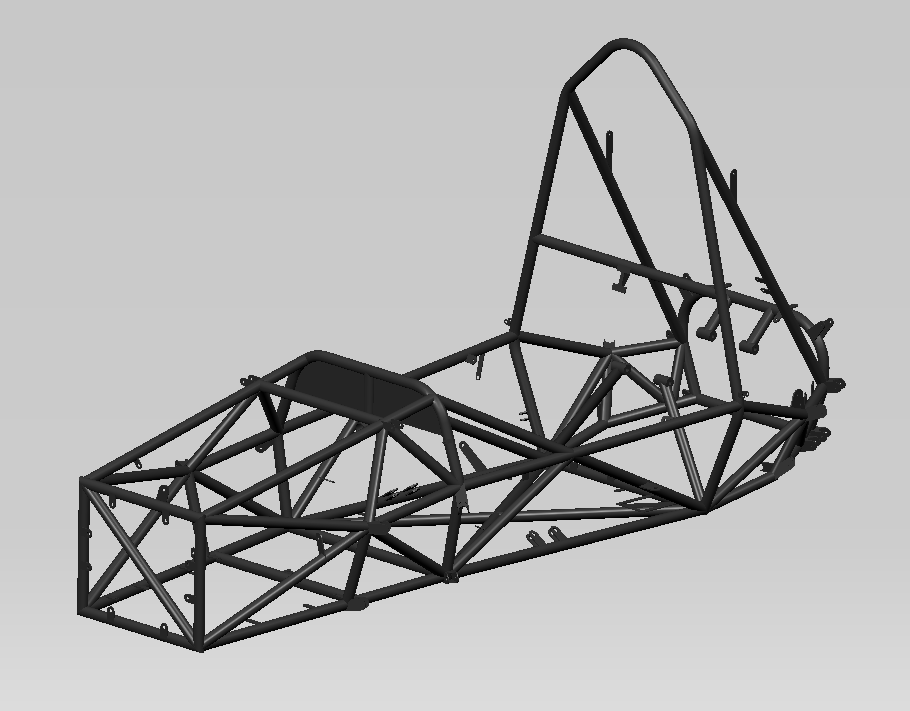
Reverse Engineering a Hair Clipper
Reverse engineering breaks down a product into its components to analyze and enhance its design efficiency, aiming to reduce costs by optimizing materials, minimizing part count, and improving assembly processes.
For this project, I redesigned a standard hair clipper to achieve these goals. Applying Design for Assembly (DFA) principles, 13 parts were eliminated by integrating features like integral springs and snap fits, cutting assembly time by 45 seconds per unit. This led to a 33% reduction in component count and a product cost reduction of $3.36 per unit, which translates to a 7.5% cost savings.
One significant design change was the redesign of the drive lever. The original design included two external springs that required compression and alignment during assembly, a time-consuming and error-prone process. To streamline this, we integrated the springs directly into the drive lever, eliminating the need for separate parts. This not only reduced the part count and cost but also cut assembly time from over 30 seconds to under 5. The Ashby chart help find a replacement material for the spring.
I developed CAD models and detailed GD&T drawings in SolidWorks, while also conducting fatigue analysis in ANSYS. Additionally, DFA and DFM analyses were performed to validate the redesign's improvements. The overall changes resulted in an annual increase in profit of approximately $672,350. Click HERE to see the detailed report.
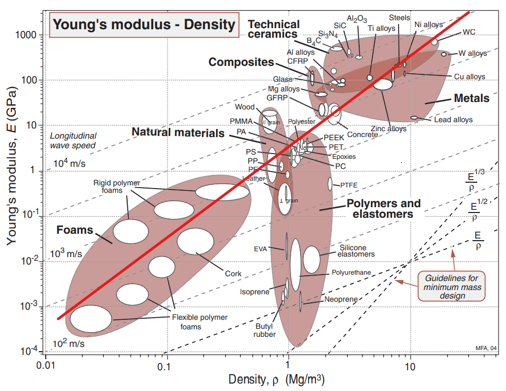
Ashby Chart helped find ABS as replacement for SS Springs
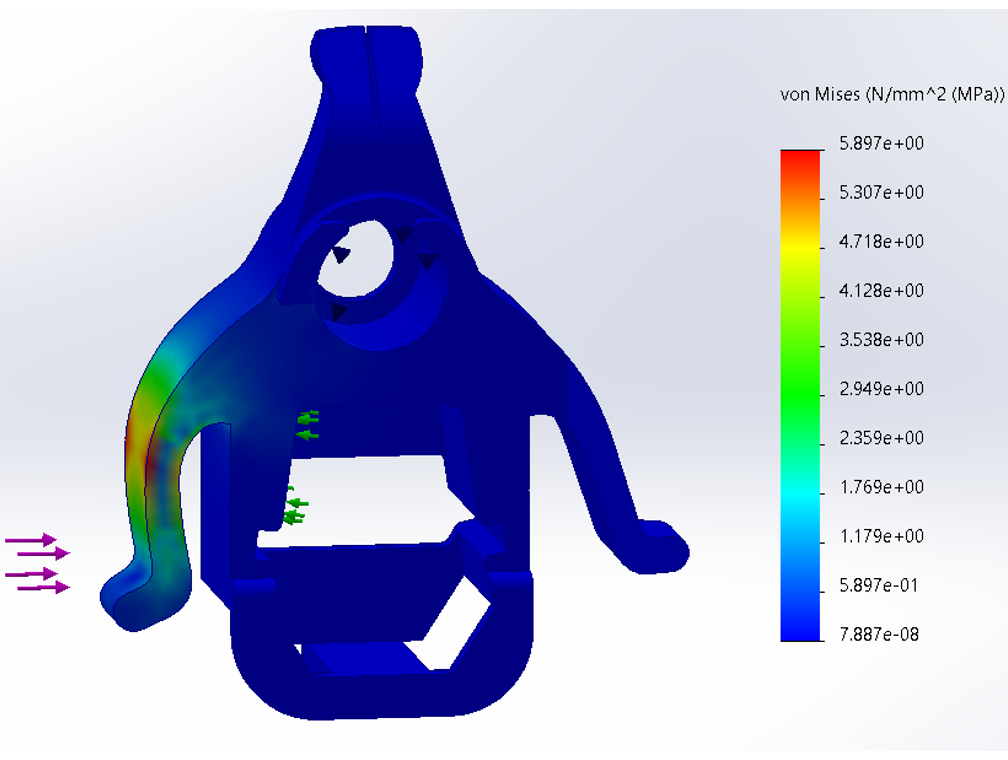
Fatigue Analysis of Drive Lever Integral Spring Redesign
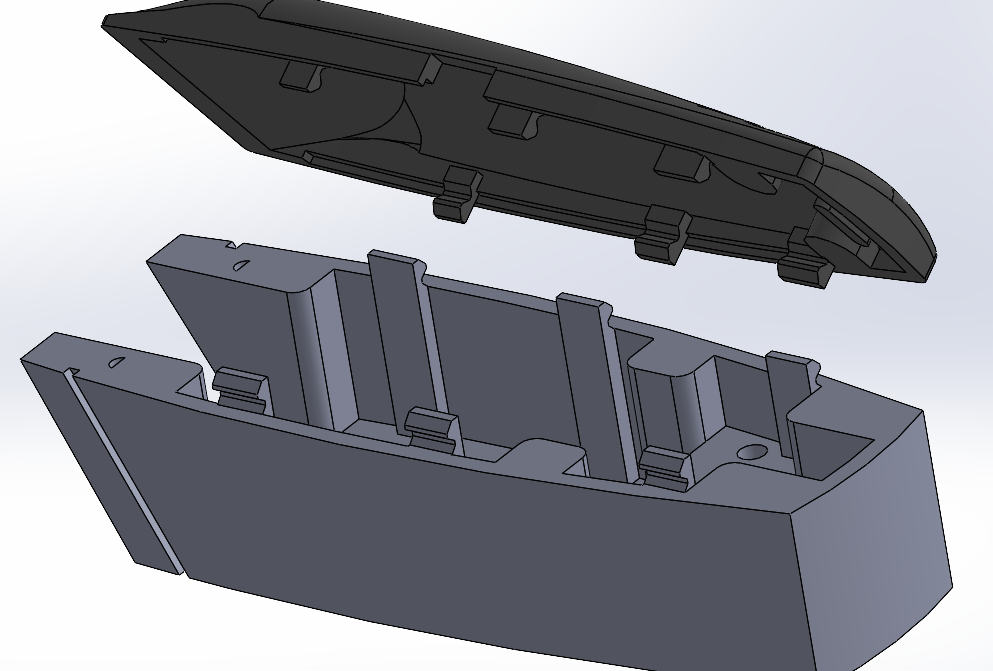
Snap Fits features for the Upper and Lower Housing
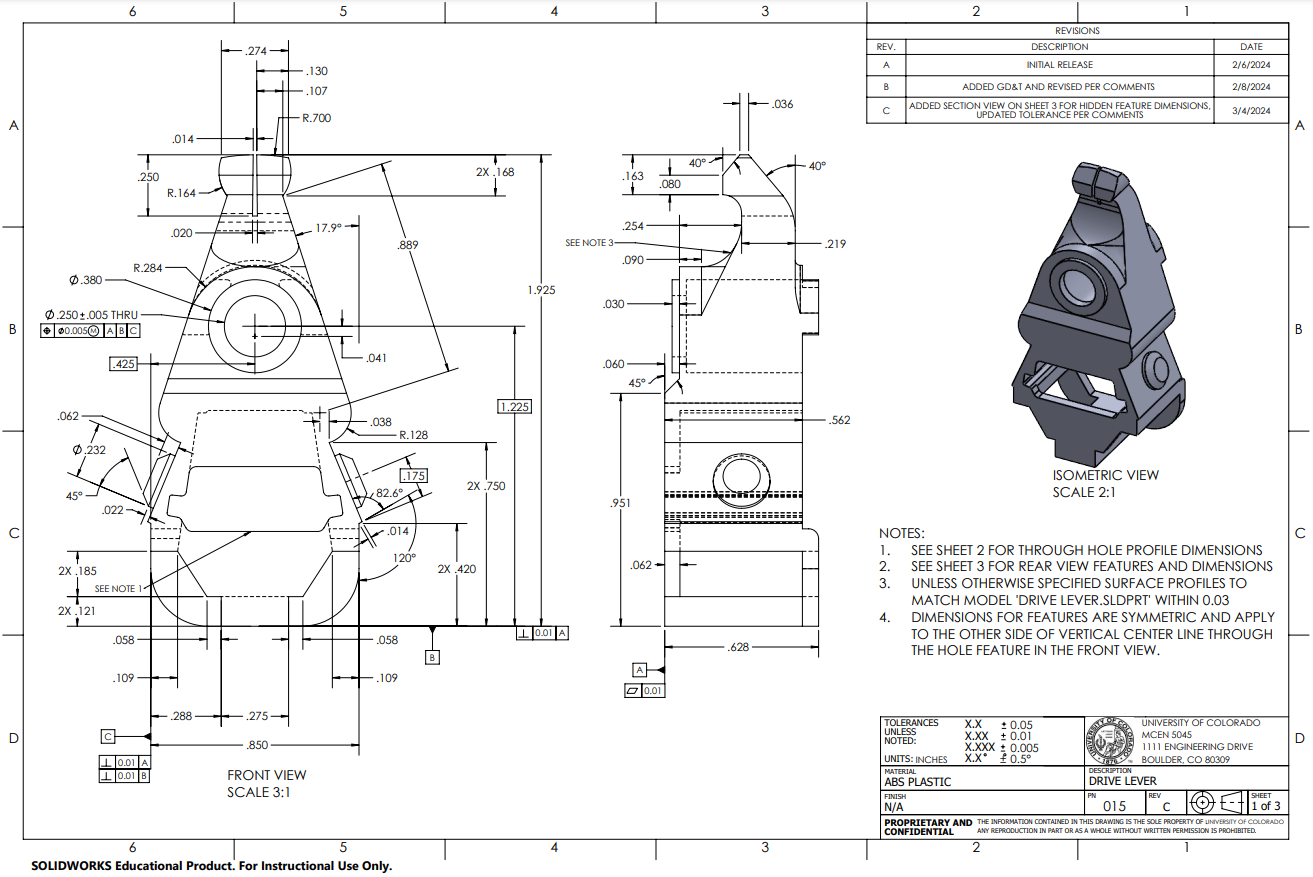
Drawing of drive Lever with detail GD&T
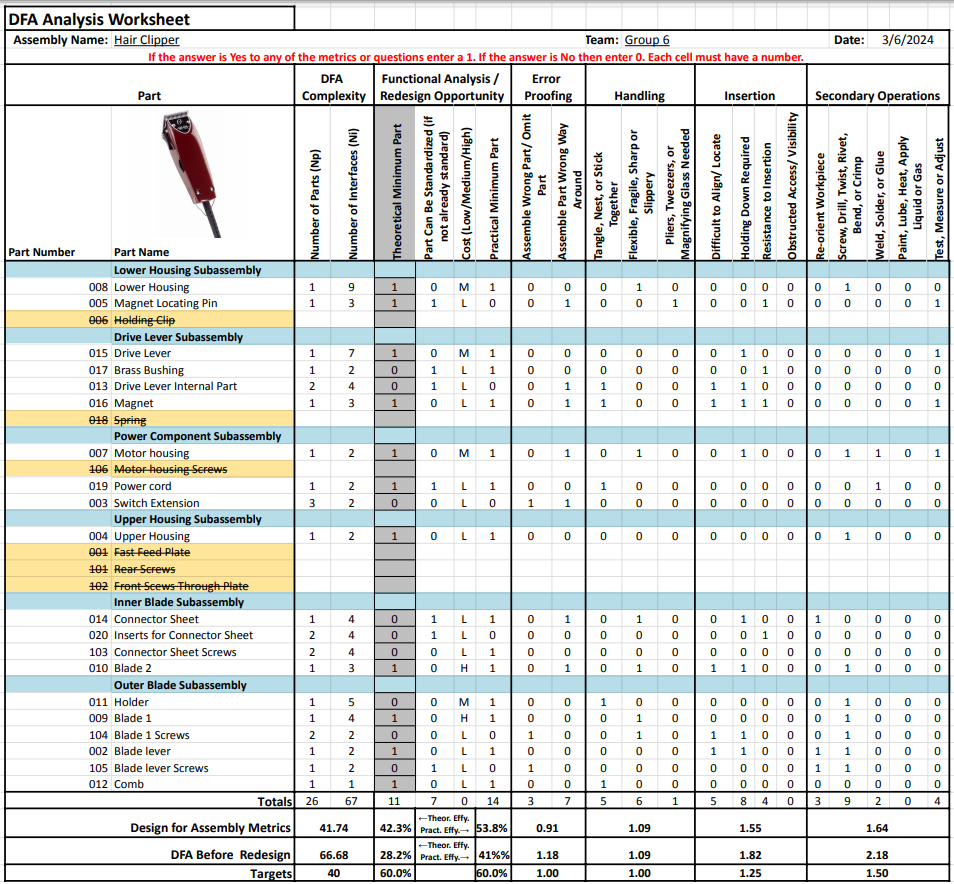
Design for Assembly (DFA) Analysis of a Hair Clipper
Top Skills Applied
My other projects
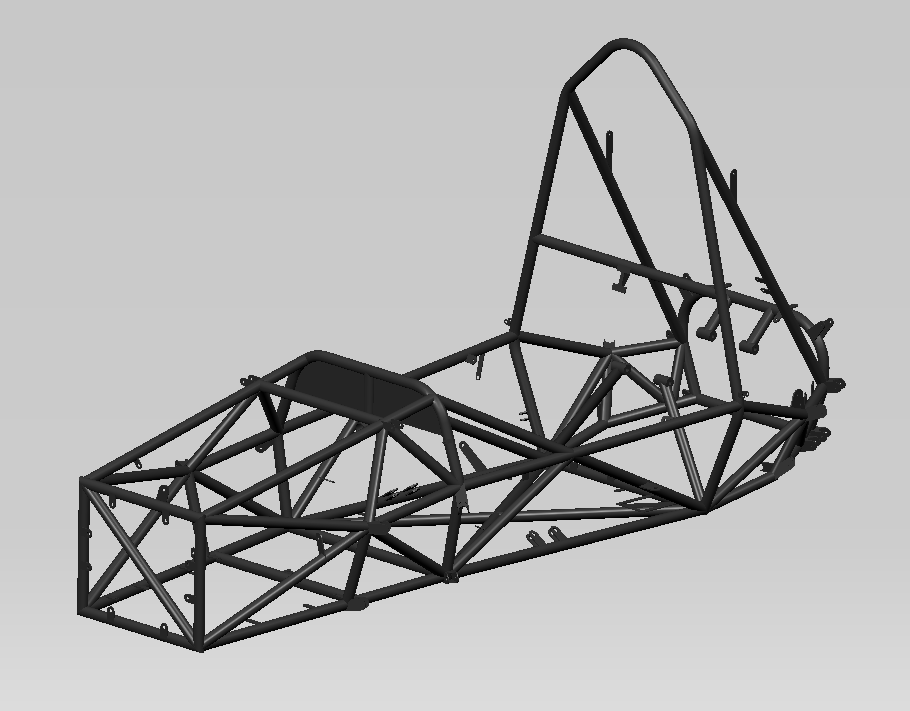
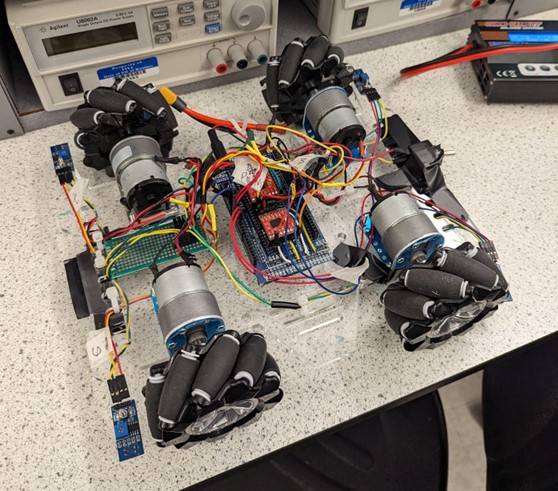
Autonomous Tank Robot
CU Boulder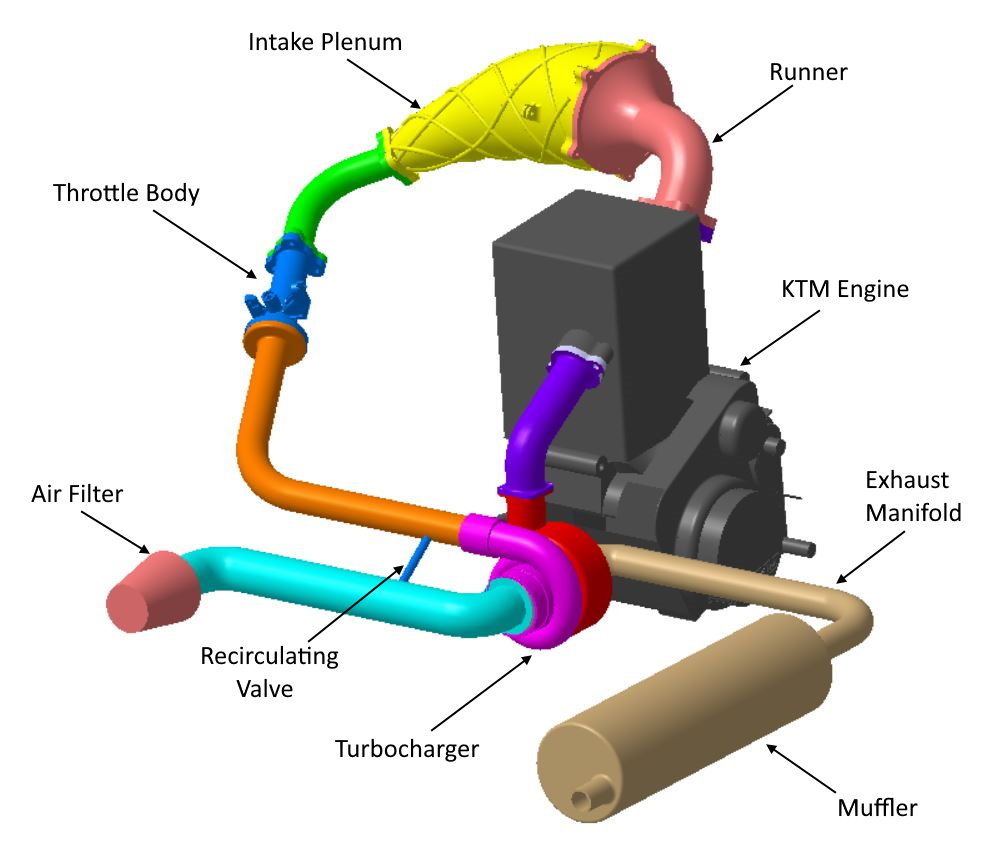